Тема 5 Биогаз
Резюме
През последните десетилетия темата за биогаза придоби по-голяма актуалност във връзка с екологичния и местен добив на електроенергия. В началото на настоящата тема се представя физико-химичната същност на биогаза. Показва се как се образува - среда и условия. Представят се две технико-технологични концепции за производство на биогаз. Първата концепция е производство на биогаз от екологична гледна точка за утилизация на органична маса, а втората за производство на биогаз за енергийни цели. Показана е принципната схема за добив на биогаз и основните съоръжения за целта. Особено внимание е отделено на суровинната база за производство на биогаз. Разгледани са основните суровини в тази насока и възможностите за добив на биогаз от тях. Дадени са биохимичните и ферментационните процеси на биомасата във ферментатора, които съпътстват биогазовото производство. Представени са основните фактори определящи метановата ферментация на биомасата - влажност, анаеробни условия, светлина, температура, химическа активност, химически състав и структура на биомасата, степен на зареждане на ферментатора.
Разгледана е принципна комплектовка на биогазова инсталация в когенеративен режим. Представени са и отделните оборудвания и системи - за складиране на биомасата, за зареждане, за разбъркване, за загряване. Показани са и газ-холдерите и различните начини за съхранение на биогаза. Разгледани са технологични режими на работа с един и два ферментатора.
Накрая е даден алгоритъм за определяне на енергийно-мощностните характеристики на биомаса при когенеративен режим на конверсия на богаза.
1.Физико-химична същност на биогаза
Биогазът представлява газова смес с високо относително съдържание на метан (СН4), получена вследствие на хидролитично разграждане и микробиолно ферментиране на високо молекулна органична материя в безкислолова (анаеробна) среда. Общият вид на биогазовия генезис може да се опише със следния израз:
Съставът и относителното съдържание на крайните компоненти в биогазовата смес се определят от значителен брой фактори, свързани със спецификата на органичната материя (биомасата), условията и технологичните параметри на хидролитичните и ферментационните процеси. Най-често количественото съотношение на газовите съставки е в следния порядък: метан (СН4) 50-80%; въглероден диоксид (СО2) 15-50%; азотни съединения (амоняк, нитрити, нитрати и др- NR) 0-7%; сероводород (H2S) 0-1%; свободен водород (Н2) 0-1%.
Калоричността (енергийното съдържание) на биогаза се определя от относителното съдържание на метана (СН4) и е най-често в интервала 22-26 МJ/m3, а обемното му тегло варира в границите от 0.650 до 0.700 kg/m3.
Високото относително съдържание на въглероден диоксид (СО2) е нежелателно, тъй като влияе негативно върху енергийните характеристики на биогаза. Завишеното му съдържание е най-често резултат от нарушаване на анаеробните условия на ферментация или от недостатъчен технологичен контрол на хидролитичните процеси в биомасата.
Сероводородът (H2S) и азотните съединения (NR) са типични съставки на биогаз, получаван от анаеробно разлагане на органична материя с високо съдържание на протеини и протеиди (отпадъци от кланици, мандри, рибни стопанства, обществени кухни и др.) Тези газови съставки нямат особено отношение към калоричността на биогаза, но влияят неблагоприятно на техническите средства за енергийната му конверсия.
2. Среда и условия за образуване на биогаз.
Естествената среда за образуване на биогаз са местата, богати на гниеща органична материя, каквито са блатата, бентосната (придънната) зона на „застойни” водни басейни, неконтролирани депа за органични отпадъци и др. Първооткривателят на биогаза е английския натуралист и енциклопедист - Шърли, който през 1677 година публикува научен труд за установена „горяща” субстанция, отделяна от повърхността на естествените блата. Тази субстанция Шърли нарича „блатен газ”, а близо 100 години по-късно, италинаският физик Александро Волта я определя като „горим въздух”. Научното обяснение за образуването на биогаза и отношението му към микробиалната ферментация е заслуга на Луи Пастьор. Разработките му инициират целенасочен добив на биогаз в изкуствено организирани и контролирани среди за ферментация на органична материя. Така през 1856 година се изгражда първата биогазова инсталация в индийското градче Мантунга в близост до Бомбай, с което е положено началото на целенасоченото производство на биогаз.
3. Фактори, налагащи организирано производство на биогаз
3.1. Енергиен глад и дефицит на фосилните енергоизточници (нефт, природен газ, въглища)
Индустриализацията и интензивния икономически растеж на цивилизацията ни са свързани с мащабна и често пъти безконтролна консумация на енергия. От една страна това води до бързо намаляване на природните енергийни ресурси, а от друга до устойчив ежегоден растеж на цените на фосилните горива (енергоизточници).
Целенасоченият добив на биогаз и последващата му енергийна конверсия е реална алтернатива на конвенционалната енергетика и потенциал за икономия на минералните енергоизточници. От физико-химична гледна точка биогазът е аналог на природния газ. Разликата е единствено в относителното съдържание на метан (СН4). В природния газ то е в интервала 95-97%, а в биогаза между 50 и 80% Средната енергийна стойност на биогаза е в границите на 4.5 до 7.5kWh/m3 [6,7], а на дизеловото гориво е приблизително 10 kWh/dm3. В този смисъл един кубически метър биогаз, получен от приблизително 1 kg органично сухо вещество на биомаса е калоричен аналог и алтернатива на около 0.6 dm3 дизелово гориво.
3.2. Екологична криза и парников ефект
Ежедневно на планетата ни се отделят милиони тонове отпадна органична материя под формата на смет, хранителни отпадъци, фекални маси, постеля (смес от животински екскременти и слама), отпадъчни води и прочие. В условията на неконтролирано депониране и естествена ферментация на тези отпадни субстрати в атмосферата се отделят милиони кубични метри метан, който представлява 3 до 5% от общото количество на парниковите емисии. Азотсъдържащите компоненти на органичната материя се минерализират и под формата на нитратно-нитритни съединения преминават в почвата и подпочвените води. Естествената микрофлора на комунално битовите отпадни води, торовата маса от животновъдството, както и технологично отпадните продукти, съпътстващи хранително-вкусовата и преработвателна промишленост са източник за бактериална контаминация на питейните води дори от сондажи с дълбочина над 30 метра.
4. Технико-технологични концепции за производство и енергийна конверсия на биогаз
В световен мащаб са обособени два основни технологични подхода (концепции) за организиран добив на биогаз. Разликата между тях е в приоритета и основната цел на непрякото минерализиране на органичната суровина заложена под формата на биомаса.
4.1.Технологична концепция за екологосъобразна утилизация на отпадна органична маса.
Основният приоритет на този подход е опазването на околната среда и поддържане на оптимална комунално-хигиенна инфраструктура. Добивът на биогаз е по-скоро технологична «опция» без особен икономически акцент. Енергийната му конверсия е чрез директно изгаряне във водогрейни котли за добив на топлинна енергия. Този модел за производство на биогаз е особено популярен за страните от югоизточна и източна Азия, където високата гъстота на населеност в комбинация със субтропичните и тропичните климатични условия налагат организирано депониране и безрискова утилизация на отпадните субстрати.
Независимо от екстензивната си специфика, тази концепция успешно би могла да се прилага в животновъдни ферми с висока концентрация на животни (например кравеферми с основно стадо над 500 животни), където ежедневният добив на торова маса предполага екологически риск.
4.2.Технологична концепция за производство на енергия от биогаз
Основният приоритет на този модел е максималният добив на енергия от единица биомаса. Екологическият аспект е на втори план и не влияе съществено върху технико-технологичните особености на изгражданите биогазови централи. Тази концепция предполага висока технологична интензивност и е присъща на биогазовото производство в държавите от централна и западна Европа. Енергийната конверсия на добивания биогаз е подчинена на формулата за едновременно производство на електрическа и топлинна енергия чрез когенератори (агрегати, състоящи се от двигател с вътрешно горене и куплиран към него електрически генератор, за добив на електрическа енергия). Поради интензивната си същност този модел за производство на биогаз не може да разчита единствено на отпадни субстрати. Нормалното му функциониране изисква целеви добив на биомаса под формата на царевица, сорго, суданка или други житно-тревни смески, подлежащи на силажиране и продължително съхранение.
5. Идеен модел за добив на биогаз
Принципът за добив на бигаз е представен със схемата от фиг.5.1
Фиг. 5.1 Принципна схема за добив на биогаз
Техническото средство, което осигурява необходимите условия за анаеробна ферментация на биомасата, се нарича ферментатор. Към него са обособени приспособления за подаване на свежа биомаса и такива за отвеждане на вече ферментиралия субстрат (биошлам в торохранилище). Всяка «порция» от заложената биомаса престоява във ферментатора между 25 и 40 дни (в зависимост от температурния режим и някои други технологични обстоятелства). В рамките на посочения период, биомасата последователно се хидролизира и ферментира (при строго анаеробни условия), отделяйки биогаз с посоченото съдържание. Следствие на анаеробната ферментация над 70% от органичните субстанции на биомасата се минерализират. Полученият (отпадният) биошлам е без типичната за органичните отпадъци неприятна миризма и е с химичен състав (калиево-форфорно-азотно съдържание) близък до този на минералните торове. След триседмичен престой в специализирано депо (балон,торохранилище,лагуна) биошламът може да се използва за целите на биологичното земеделие. Екологичният и комунално-хигиенният риск са сведени до минимум, тъй като колибактериалната обсемененост е средно до 10 микроорганизма на 1g сухо вещество (при норма 1000 бр.), а салмонелна и стрептококова контаминация липсва.
6. Суровинна база за произвоство на биогаз
Изходната суровина за производството на биогаз се нарича биомаса. В зависимост от произхода си може да се класифицира на първична (целево отглеждана) и вторична (отпадна) биомаса. В таблици 5.1, 5.2, 5.3, 5.4 [5,6,7] са представени продуктовите и енергийните характеристики на основно използваните в практиката на биогазовото производсво органични маси.
Табл.5.1 Характеристики на някои основни суровини за производство на биогаз /за 1t суровина/
Табл.5.2 Средна газова продуктивност на някои видове технологични отпадъци
Пояснение към абревиатурите:
СВ - сухо вещество в %
°СВ - органично сухо вещество в % от количеството СВ
*** - средно за всички видове растителни отпадъци, свързани с
производството цветарството, градинарството, оранжерийното
производство.
Табл.5.3 Продукти от течен животински тор при биогазово преобразуване
Табл.5.4 Продукти от препоръчителни земеделски култури при биогазово преобразуване
От групата на първичната биомаса с най-голямо значение за практиката е царевичният силаж при млечно восъчна зрелост, тревните смески за силажиране и фуражното цвекло.
От подгрупата на растителните отпадъци с условна пригодност за използване са сламата от житните култури и царевичака. Високото им целулозно съдържание и някои от физико-механичните им специфики усложняват предварителната обработка на биомасата и водят до проблеми с отделянето на биогаза от повърхността на субстрата във ферментатора. Растителни отпадъци с висока степен на лигнификация (дървесни отпадъци, лозови пръчки и други дендромаси) са неподходящ субстрат за целите на биогазовото производство.
От групата на вторичната биомаса с най-голямо значение за практиката е свежата тор от говедовъдството и свиневъдството. Това е основният аргумент за технологичното „обвързване” на земеделието (в частност животновъдството) с интензивните технологии за добив и енергийна конверсия на биогаз.
Отпадните продукти от месо и млекопреработвателната индустрия са с условна пригодност за производство на биогаз. Високото им протеиново съдържание предполага ръст на сероводорода и нитратните компоненти на биогазовата смес. Същите влияят неблагоприятно върху техническите средства (двигателя с вътрешно горене на когенератора) за енергийно усвояване на биогаза. От друга страна за спазване на регламентираните хигиенни изисквания тези субстрати се подлагат на допълнителна обработка преди залагането им във ферментатора (най-често пастьоризация или стерилизация), което оскъпява оборудването и цялостното производство на енергия.
7. Биохимични и ферментационни процеси на биомасата във ферментатора.
Процесът на образуване на биогаз предполага поредица от биохимични и микробиологични процеси в субстрата на базата на твърде сложна симбиоза между различни микроорганизми. Принципът на биохимизма и микробиалната кинетика са представени със схемата от фиг. 5.2.
Фиг. 5.2. Биохимизъм и микробиална кинетика на биомасата.
В най-общ вид непрякото анаеробно окисляване на биомасата преминава през три основни фази [2,3,5,8].
В рамките на първата фаза, под действието на микробиални ензимни комплекси, макромолекулните съединения на биомасата се хидролизират до ниско-молекулни компоненти - дизахариди, монозахариди, пептиди, свободни аминокиселини, мастни киселини и др. Динамиката на хидролитичните процеси се влияе силно от физикомеханичната структура на биомаса и водноелектролитния баланс в цялостния субстрат.
На втората фаза, с участието на киселиннообразуващи бактерии ниско-молекулните органични компоненти (получени от хидролизата на биомасата) ферментират до различни по вид органични киселини (млечна, оцетна, маслена, валерианова, изовалерианова и прочие) и алкохоли.
В резултат на това реакцията на средата в субстрата е леко кисела - рН≈4.5÷6.0.
От технологична гледна точка продължителността на втората фаза е необходимо да се понижава контролирано. Адекватното редуциране на „киселинната” фаза намалява относителното съдържание на въглероден диоксид (СО2) в биогаза, влияе благоприятно на рН в субстрата и ускорява метаногенезата.
Третата фаза се активира при наличието на подходящ хранителен субстрат и съдържание на кислород под 2%. Тя протича в следствие на ферментационните процеси от близо 10 вида метанококи и метанобактерии. В резултат на това свободните органични киселини и алкохола ферментират до метан (СН4) и свободен водород (Н2). Съдържанието на получения биошлам се определя от минералния състав на биомасата и неразтворимите органични съединения, получени през трите фази на непрякото окисление на субстрата.
Биохимичните процеси и динамиката на микробиалната флора в биомасата имат отношение към технологичните режими и начина на свързване на ферментаторите.
8. Фактори, определящи метановата ферментация и производството на биогаз.
Ефективното производство на биогаз с високо метаново съдържание се определя от въздействието на редица фактори[1,5,9,11,12].
8.1 Влажност (съдържание на вода) на биомасата. В практиката на биогазовото производство са установени три основни технологични режима в зависимост от влажността на ферментиращия субстрат.
✔ Режим на течна ферментация. Това е основният технологичен подход за интензивно производство на биогаз от отпадна органична маса (течна или полутечна животинска тор) и целево отглеждани земеделски култури (царевица, сорго, суданка, житно-тревни смески и др.). Съдържанието на сухо вещество (СВ) в биомасата е до 20-22% (респективно влажността е 78-80%). Производството на биогаз от субстрати с влажност над 90% е неефективно и с ниско метаново съдържание. Оптималната концентрация на сухо вещество в биомасата при течния режим на ферментация е в диапазона 12-18% (влажност 82-88%).
✔ Режим на полутечна ферментация.
Съдържанието на сухо вещество във ферментиращия субстрат е над 22% и може да достигне до 50%. Този технологичен режим е със сравнително ограничено приложение поради високите енергийни разходи за миксиране на субстрата и технически ограничения с отвеждането и последващата утилизация на биошлама.
✔ Режим на суха ферментация.
Този технологичен подход е адаптиран за екологично утилизиране на битови и комунални отпадъци с високо съдържание на органична маса. Сухото вещество на депонираните субстрати е най-често около и над 50%. Същите се заравят в предварително подготвени подземни депа (фиг.5.3), уплътняват се и след определен период от време (от няколко месеца до 1-2 години) започва отвеждане на образувания в сметното депо биогаз [1,5].
Фиг.5.3 Принципна схема за производство на биогаз от твърди битови отпадъци
Методът за производство на биогаз от твърди битови отпадъци изисква огромни площи и инвестиции. В този смисъл той не е „атрактивен” за частните предприемачи в областта на земеделието. Реализацията му е по-скоро обект на проекти по линията на публично и публично-частно партньорство, с основна цел - екологична утилизация на битови и комунални отпадъци.
8.2. Поддържане на строго анаеробни условия за ферментация.
Метановата ферментация протича при строго анаеробни условия. Тя се активира при относително съдържание на свободен кислород (О2) в субстрата под 2%. Кислородното съдържание над посочения лимит „измества” микробиологичната динамика в посока на киселинно-образуващите бактерии. Резултатът от подобна ферментационна среда е добив на биогаз с високо съдържание на въглероден диоксид (СО2) и ниска метанова концентрация.
8.3. Светлина.
Светлината не е бактерициден фактор за метанобактериите, но значително намалява метаболизма им. Това налага материалите, с които се изграждат ферментаторите, да бъдат оптично непроницаеми (в това число и полимерните мембрани за интегрирано съхранение на биогаза в обема на ферментатора).
8.4. Температурни условия.
В практиката за производсво на биогаз са установени три температурни режима, от които два са технологично значими.
✔Психрофилен режим.
Температурата на биомасата е до 20°С. Ферментационната динамика на психрофилните бактериални щамове е относително ниска, а добивът на биогаз е неефективен и нерентабилен. Психрофилният режим е с ограничено приложение и е практически обоснован за региони с ниски средногодишни температури.
✔ Мезофилен режим. (фиг.5.4)
Фиг.5.4 Влияние на температурата върху добива на биогаз [5]
Температурата на биомасата е в диапазона от 25 до 40°С. Добрите практики за биогазово производство при мезофилен режим се реализират при температура 34-37°С. Това налага ферментаторите да бъдат топлоизолирани. В този диапазон, технологичната продължителност за пълно ферментиране на биомасата е около 35-40 дни. В рамките на този период, биогазовото производство е равномерно със сравнително ниско ускорение на микробиалната активност през първата и последна седмица от работния цикъл (фиг.5.5). Добиваният биогаз е с високо относително съдържание на метан (СН4).
Фиг.5.5 Динамика на газообразуването при мезофилен и термофилен режим [5]
✔ Термофилен режим.
Реализира се при температура на биомасата в диаозона между 40 и 55°С. Ферментационните процеси са динамични с високо положително и отрицателно ускорение в началните и крайните дни от работния цикъл (фиг.4.5). Средната технологична продължителност за пълна ферментация на субстрата е между 25 и 30 дни, което дава възможност при едни и същи мощности (с мезофилния режим) да се намалят обемите на ферментаторите. Тенденциите в развитието на биогазовото производство са насочени към преминаване на ферментаторите от мезофилен към термофилен режим, независимо от вероятността за известен технологичен риск. Термофилната ферментация изисква „връщане” на значителна част от добитата топлинна енергия, с оглед на поддържането на температурния режим в диапазона около 45°С. Термофилните бактериални щамове са термочувствителни и температурните колебания в биомасата над 2-3°С намалят ферментационната им активност. Това налага ферментаторите с термофилен режим на работа да бъдат с необходимото топлоизолационно покритие.
Необоснованото покачване на температурата над номиналния праг за даден бактериален щам (с оглед скъсяване на технологичния престой на биомасата във ферментатора) води до нарастване съдържанието на въглероден диоксид в биогаза за сметка на метановото му съдържание.
8.5. Химическа активност (рН) на средата във ферментаторите.
Химическата активност (рН) на биомасата във ферментатора трябва да бъде неутрална с индикации за слабо алкална активност (рН≈7.5). Този режим трябва да се установи максимално бързо (още през първата седмица на ферментация) с оглед на биогазово производство с високо метаново съдържание. Понижаването на рН на биомасата под 7.0 влияе отрицателно както на абсолютното газово производство, така и на метановата концентрация (фиг.5.6).
Фиг.5.6 Процес на образуване на биогаз, състав на газа и промени в pH [5]
При използване на биомаси с висока начална киселинност е необходимо добавяне на буферни или алкализиращи коферменти с оглед бързото установяване на неутрална среда във ферментатора.
8.6. Степен на зареждане (натоварване) на ферментатора.
Степента на зареждане на ферментатора влияе върху интензивността на биогазовото производство и продължителността на технологичния „престой” на биомасата (фиг.5.7).
Фиг.5.7 Влияние на степента на зареждане на ферментатора върху газопроизводството [5]
Непълното натоварване (зареждане) на ферментатора редуцира среднодневния добив на биогаз и удължава продължителността на времето за пълна ферментация на субстрата.
Режимът на зареждане на ферментатора корелира с химическата активност (рН) на средата му. Непълното му натоварване води до понижаване на рН и установяване на киселинна активност. Това предполага нисък добив на биогаз с незадоволителна метанова концентрация.
8.7. Химически състав на биомасата.
Оптималният добив на биогаз се влияе силно от въглерод-азотното съдържание на използваната биомаса. Добрите практики показват, че максималните добиви на биогаз се реализират при субстрати, в които на една обемна единица азот съответстват 10-15 единици въглерод. По-високото въглеродно съдържание (1:20÷25) понижава рН на средата и инхибира (подтиска) метаногенната флора.
8.8. Физико-механична структура на биомасата.
Неразтворимите във вода органични вещества трябва да бъдат механично раздробени при препоръчителна едрина на частиците между 5-10 mm. Използването на високомаслени коферменти изисква предварително емулгиране на съдържащите се в тях мазнини. Физико-механичната кондиция на биомасата определя контактната й повърхност и по този начин влияе индиректно върху продължителността на технологичния престой във ферментатора.
9. Принципна схема и комплектовка на биогазова инсталация с когенеративен експлотационен режим.
На фиг.5.8 са представени панорамния вид и принципната комплектовка на биогазова инсталация, интегрирана към производството на животновъдна ферма.
Фиг. 5.8 Принципна схема на биогазова инсталация в когенеративен режим
Основният кофермент на биомасата е животинската тор, която постъпва в приемната шахта на инсталацията. При необходимост, към торовата маса могат да бъдат подавани допълнителни коферменти (например царевичен силаж) с оглед повишаване на биогазовия добив. С помощта на помпен агрегат за гъсти течности или чрез механичен транспортьор „дневната доза” биомаса се подава във ферментатора. Температурният режим на средата му се поддържа от топлообменник за сметка на произведената от когенератора топлинна енергия. Добитият биогаз се съхранява в газхолдерен купол (камера), интегриран към горната част на ферментатора, откъдето се подава към двигателя с вътрешно горене на когенераторния модул. Куплираният към двигателя генератор произвежда променливо-токова електрическа енергия, която се симфазира с честотата на електропреносната система, трансформира се в подходящо напрежение и се подава към енергосистемата.
Охладителната система на ДВГ на когенератора е свързана с външен топлообменник, през който циркулират антифризът от водните ризи и междинният топлоносител (виж фиг.5.10). Последният отнема топлината от охладителната система и през втори топлообменник я прехвърля и акумулира под формата на топла вода за битови и технологични цели.
Част от добитата топлинна енергия се подава обратно към ферментатора за поддържането на постоянен температурен режим на ферментация.
При така наречените тригенеративни модули част от добитата топлинна енергия се подава към абсорбционен тип охладителна машина. За сметка на приведената топлина, абсорбционната машина генерира охладителна енергия (студ), който може да се използва за климатизация на помещения или други технологични приложения.
10. Технико-технологично оборудване на биогазови инсталации.
Ефективното производство на биогаз може да се реализира единствено при подходящо подбрани технически средства, осигуряващи необходимите параметри на метаногенните фактори.
10.1. Депа за биомаса.
Представляват различни строителни съоръжения за временно съхранение на компонентите на биомасата. Техническата им специфика зависи от органичния състав и физико-химичните свойства на съответния кофермент.
✔ Приемни (колекторни) шахти за течна или полутечна животинска тор (най-често говежда)( сн.5.1).
Сн.5.1 Приемни шахти
Представляват стоманобетонови съоръжения с наземно или вкопано (подземно) изпълнение. Подаването на торовата маса към шахтите може да се реализира гравитачно, мобилно-транспортно (торова цистерна) или чрез помпен агрегат. Основното изискване към шахтите е да бъдат хидронепроницаеми по отношение на подпочвените води. Полагането на покривна конструкция е препоръчително, тъй като намалява разпространението на неприятна миризма и ограничава аеробното ферментиране на тора. В този смисъл особено надеждни са т.нар. „балон-лагуни”, които осигуряват херметично съхранение на биомасата до залагането й във ферментатора .
✔ Силажни траншеи (сн.5.2)
Сн. 5.2 Силоз за биомаса към инсталация за биогаз
Тези съоръжения са задължителни за всички биогазови инсталации, при които в биомасата се добавя силаж от царевица или други житни култури. Дъното и страничните ограждащи стени на траншеите се изпълняват от стоманобетон с повърхностно добавен противокиселинен пластификатор. Технологиите за силажиране на биомасата не се различават от тези за производството на фуражен силаж. Изваждането на силажа от траншеята и подаването му към приемната шахта се извършва най-често чрез фрезов товарач и мобилни транспортни машини. В технологичен аспект най-подходящи са прикачните или самоходните миксер вагони, тъй като осигуряват дозирано „самотоварене”, допълнително нарязване, транспорт и подаване на масата в приемната шахта
✔ Закрита складова база. (сн. 5.3)
Сн. 5.3 Закрита складова база за коферменти
Представляват атмосферно-затворени помещения с универсални строително конструктивни решения. Предназначени са за съхранение на коферменти (в т.ч. и буферни компоненти за стабилизиране на рН във ферментаторите) в насипно-пакетирано състояние. Към складовата база може да бъде интегриран пункта с контролно-автоматичната апаратура за мониторинг, контрол и управление на технологичните процеси в инсталацията.
10.2. Технически средства и технологични методи за кондициониране (предварителна подготовка преди зареждане във ферментатора) на биомасата.
Основното предназначение на тази категория оборудване е надробяване, миксиране и хомогенизиация на биомасата (или на отделни нейни компоненти) преди подаването й към ферментатора. Тези технически съоръжения са най-често интегрирани или инсталирани в непосредствена близост с приемните шахти. В зависимост от физикомеханичната методика за кондициониране на коферментите, оборудването се класифицира в следните видове:
a Технически съоръжения за термична дезинтеграция (сн. 5.4)
Сн. 5.4 Автоклав за термична обработка при високо налягане
Методът и съоръженията за термична дезинтеграция са присъщи за предварителна обработка на субстрати, изискващи пастоьоризация (отпадъци от кланици, хранително-вкуови предприятия и др.). Термичната дезинтеграция се осъществява в херметично затоворени съдове, работещи под налягане - автоклави. Технологичният режим на обработка протича при температура от 160 до 200°С и налягане над 20 bar с продължителност 30-60 min. В условията на това въздействие над 70% от органичната маса се хидролизира и превръща в своеобразен „хранителен бульон” за директно ферментиране от метаногенните бактерии. Този подход води до чувствително редуциране на първа и втора фаза на биохимичната и микробиална кинетика в биомасата и способства образуване на биогаз с много високо метаново съдържание (над 75% СН4).
✔Технологичен метод за химична дезинтеграция.
Методът е актуален при биогазови инсталации в биомаса, на които се включват растителни субстрати богати на фибри (влакнини) и с висока степен на лигнификация - слама, царевичак, слънчогледови стъбла и др. Технологията се свежда до третиране на субстратите с разтвор на натриева основа (NaOH) в условията на контролирано загряване. Ефектът е ускорена хидролиза на целулозо- и хемицелулозните компоненти до ниско-молекулни органични комплекси, които се усвояват последователно от киселинните и метаногенните бактерии.
✔ Технологичен метод за ултразвукова дезинтеграция.
Това е сравнително иновационен метод в практиката на биогазовото производство. Реализира се чрез ултразвукови генератори, работещи в честотен диапазон над 20кНz (килохерца). Подаденият ултразвук предизвиква ефект на кавитация върху граничната повърхност на твърдите субстратни частици и течната фаза на биомасата. В резултат на това започва равномерно дезинтегриране (разрушаване) на корпускуларните коферменти.
11. Технико-технологични средства за зареждане на биомасата във ферментаторите.
Тази част от комплектовката на биогазовите инсталации се отличава с огромното си разнообразие от технологични решения и технически средства. Конкретният им избор се определя основно от вида на биомасата, конструктивната специфика на останалите системи за оборудване и общата специфика на утвърдената методика за добив на биогаз.
11.1. Технологичен режим и технически средства за хидравлично зареждане на ферментаторите.
Режимът е изключително подходящ за биогазови инсталации, работещи на биомаса с преобладаващо съдържание на течна или полутечна животинска тор. Техническата реализация е чрез роторни електропомпени агрегати, които се инсталират в или непосредствено до приемната шахта. При наличие на постелъчен материал в тора (слама, стърготини и др.) или при добив на растителни коферменти, към ротора на помпата се монтира нарязваща секция (биорезачка) (сн. 5.5).
Сн. 5.5 Ротационна помпа в комбинация с „биорезачка”
С помощта на трипътен потоко-управляем модул роторната помпа първоначално миксира, нарязва и хомогенизира биомасата в обема на самата шахта. След постигане на подходящата кондиция на субстрата, трипътния модул „обръща” потока и през специален (автоматично управляем) шибър, помпата транспортира биомасата от приемната шахта към ферментатора. Роторните помпи в комбинация с биорезачки са изключително подходящо решение за биогазови инсталации, използващи системи за подгряване на субстрата с помощта на „външни” (монтирани извън обема на ферментатора) топлообменни апарати. Подобна интеграция опростява режима за вътрешно разбъркване на биомасата, тъй като помпеният агрегат осигурява хидравлично миксиране на субстрата при периодичната му циркулация през външния топлообменник.
11.2. Технологичен режим и технически средства за механично зареждане на ферментаторите.
Този технологичен подход е присъщ за биогазови инсталации, при които към биомасата се добавят растителни (или друг вид) коферменти в насипно състояние - най-често силаж от царевица или други житно-тревни смески. Основният елемент на механичните средства за зареждане е винтов транспортьор с оределен режим на задвижване и подаване на субстрата.
✔ Мобилни транспортьори.
Представляват най-често прикачни фуражосмесителни вагони (ремаркета) с общо технологично предназначение , към бункера на които се куплира винтов транспортьор.
Машините са с мобилен режим на зареждане и се агрегатират към трактори от среден теглителен клас. Зареждането на биомасата във ферментатора е „горно” (над нивото на субстрата), което олекотява хидравличната херметизация на реактора. Транспортьорът се куплира директно към зареждащия шибър, без необходимост от допълнително автоматично синхронизириране между режима на подаване на субстрата и положението за шлюзовата клапа (шибъра). Използването на мобилни винтови транспортьори е удачно за зареждане на ферментатори със сравнително не голям обем (до 500 м3), монтирани и експлоатирани в условията на действащи животновъдни ферми.
✔Стационарни винтови транспортьори.
Стационарният винтов транспортьор е най-често с диаметър 500 mm. Задвижва се чрез планетарен редуктор, агрегатиран към електродвигел с мощност 4-10 кW (сн.5.6).
Сн. 5.6 Стационарен винтов транспортьор с приемна фуния (горно подаване)
Транспортьорът може да се инсталира и куплира към зареждащия шибър на ферментатора като осигурява режим на „долно” подаване на биомасата(сн.5.7).
Сн. 5.7 Пресуващ транспортьор за долно зареждане
Хидравличната клапа между ферментатора и транспортьора е възвратна и се отваря при създадено от винта налягане по-голямо от хидростатичното на субстрата. Пълната херметизация на свръзката се гарантира от междинен шибър, чието положение се синхронизира с винтовия ефект на транспортьора.
Технологичната концепция за „долно” зареждане със стационарен транспортьор е подчинена на максимата за строги анаеробни условия на ферментация. Този режим за подаване на субстрата свежда до минимум навлизането на атмосферен въздух в обема на ферментатора. Оборудването на стационарния вариант е специаилизирано, което предполага инвестиционен формат, подходящ за биогазови централи с високи мощности, оборудвани с ферментатори над 1000м3 работен обем.
12. Ферментатори (биореактори) за анаеробна ферментация и добив на биогаз.
Ферментаторът е основният компонент в комплектовката на всяка биогазова инсталация. Той представлява херметически затворена камера, изградена от хидро- и светлонепроницаеми строителни материали. Изгражда се върху специално бетонирана площадка с наземно изпълнение. В региони с „пресечен” (хълмист или планински) релеф е възможен строителен вариант за частично или пълно вкопаване на ферментатора под повърхността на земнопочвения терен. Подобно решение не е препоръчително за изграждане на мащабни биогазови инсталации, в мегаватовия мощностен диапазон.
В зависимост от вида на строителните материали и начина на изграждането им, ферментаторите се делят на две основни категории.
12.1. Бетонови ферментатори.(сн. 5.8).
Сн. 5.8 Бетонов ферментатор с топлоизолация
Изграждат се от стоманобетон с допълнителна добавка на киселинноустойчиви пластификатори, осигуряващи антиерозивна устойчивост на вътрешните повърхности, контактуващи с химично реактивната среда на биомасата. Термостабилността на ферментаторите се осигурява от външна топлоизолация, изпълнена от полистиренови, полистиролови или полиуретанови плоскости с повърхностно положена хидроустойчива замазка. При масово изгражданите варианти, горната основа (покрива) на ферментатора се изпълнява от дървена или пластмасова решетка, над която се свръзва полимерната мембрана на газхолдерния купол (камерата за временно съхранение на биогаза).
12.2. Стоманени ферментатори. (сн.5.9).
Сн. 5.9 Стоманен ферментатор в процес на изграждане
Изграждат се от дъговидни сегменти, изработени от легирана корозионно устойчива стомана V2A и V4A. Цялостната конструкция се инсталира върху предварително фундирана стоманобетонова площадка. Топлоизолационното покритие и изпълнението на газхолдерния купол са аналогични на бетоновите ферментатори (виж т.12.1).
13. Системи и съоръжения за загряване /темпериране/ на ферментаторите.
Ефективното биогазово производство се реализира при условия на мезо- или термофилен режим. Това налага част от добитата по когенеративен път топлина да се „върне” и чрез подходяща топлообменна инфраструктура да се предаде на биомасата с оглед температурата й да бъде в необходимия диапазон (35-37°С или 45-50°С).
В зависимост от начина на изпълнение и конструкцията на топлообменната инфраструктура, системите за темпериране на ферментаторите биват няколко вида.
13.1. Водно-отоплителна система, интегрирана (вградена) към стената на ферментатора. (сн.5.10).
Сн. 5.10 Полимерни подгряващи тръби и арматура в стената на бетонов ферментатор
Вариантът се изпълнява от специализирани „многослойни” (РехАl) или полимерни тръби, опасващи външната страна на ферментатора под формата на хоризонтален растер. През обособената тръбна мрежа и топлинния акумулатор на когенератора, циркулира принудително топлоносител (вода или антифриз). Топлообменът е индиректен през стените на тръбната мрежа и тези на ферментатора. Топлозагубите към околната среда се ограничават от топлоизолационното покритие на ферментаторите.
Описаната система е особено подходяща за темпериране на бетонови ферментатори. Условно приложима е за биореактори от легирана стомана. Основното преимущество на водно-отоплителния вариант е високата му надеждност, продължителния експлоатационен живот и сравнително ниския инвестиционен мащаб. Известно ограничение за системата се явява инертността на топлообменните процеси при евентуална промяна в температурните потенциали на биомасата и топлоносителя.
13.2. Система за вътрешно подгряване на биомасата от тръбни топлообменни тела. (тип „лира”) (сн. 5.11)
Топлообменната инфраструктура представлява редуващи се по височина метални тръби/серпентини/, които „опасват” вътрешната страна на ферментатора. Тръбната конструкция се изработва от антикорозионнно легирана стомана V2A или V4A, монтирана конзолно във вътрешността на биореактора. През обособена „тръбна” лира и топлоакумулатора на когенератора циркулира принудително работния топлоносител. Повърхността на стоманените тръби извършва директен топлообмен с биомасата, което снижава инертността на процеса. Технологичното ограничение на металните лири е свързано с надеждността на корозионната им устойчивост и вероятността от повърхностно отлагане на частично минерализиран субстрат, намаляващ топлопроводността им.
13.3. Система за индиректно подгряване на биомасата чрез външен топлообменен модул.(сн.5.12).
При този технологичен вариант подгряването /темперирането/ на биомасата се извършва извън обема на ферментатора. За целта се инсталира „пластинчат” или кухотръбен тип топлообменник, осигуряващ хидравлично изолирана циркулация на субстрата от ферментатора и работния флуид от топлинния
Сн.5.12 Външен топлообменен модул за подгряване на биомасата
акумулатор на когенератора. Топлообменникът между двата потока е индиректен, през термопроводните стени на модула. Системата е интегрирана към помпения агрегат за зареждане, нарязване и хидравлично миксиране на биомасата, т.е. процесът на темпериране протича успоредно с останалите операции. Потокът на работния флуид от топлинния акумулатор на когенератора се осъществява от независима циркулационна помпа, чието управление е синхронизирано с това на основния помпен агрегат.
Основното преимущество на описания метод е точността за регулиране на температурния режим и високата ефективност на топлообменния процес. Външното (по отношение на ферментатора) инсталиране на топлообменния модул дава възможност за постоянен достъп, контрол, профилактика и сервизиране на съоръжението. Основното технологично изискване за нормална експлоатация на системата е биомасата да не съдържа влакнести структури и компоненти с едрина над 5 mm.
14. Технологични режими и технически средства за миксиране (разбъркване) на биомасата.
Целта на тази конструктивна комплектовка е да се осигури хомогенизация на субстрата, равномерен температурен градиент в целия му обем, равновесие на рН (химическата активност), бърза бактериална контаминация на „прясно” подадената маса и безпрепятствено отделяне на образувания биогаз към камерата на газхолдера[12].
В зависимост от вида на техническите средства и режимът им на работа се използват няколко варианта за миксиране на биомасата.
14.1. Нискооборотни механични миксери с постоянно действие.
Разбъркващият механизъм е витлов (пропелерен)(сн.5.13)
Сн.5.13Винтов(пропелерен) разбъркващ механизъм
Сн. 5.14 Лопатков разбъркващ механизъм
Инсталира се радиално във вътрешността на ферментатора, лагерувайки в стената му и в допълнителна колонна конзола. Задвижващата мотор-редукторна станция се монтира външно върху постамент към стената или горната част на ферментатора (сн.5.15).
Витловите и лопатковите миксери са най-често с режим на постоянно действие при честота на въртене 30-40 min-1 (оборота в минута) и изискват ел. задвижване с мощност 10-20кW. По периферията на пропелерите или лопатките могат да се монтират допълнителни твърдосплавни режещи пластини за наситняване на субстрата. Нискооборотните миксери са адаптивни
Сн. 5.15 Външно (на биореактора) разположен двигател на разбъркващ механизъм
към всички видове ферментатори, но са препоръчителни за биогазови инсталации, работещи с биомаса, богата на влакнини и фибри (слама, царевичак и др.).
14.2. Високо оборотни (интензивно действащи) миксери с периодично действие.
Тези варианти са „потапящ” тип и се монтират във вътрешния обем на ферментатора, в близост с дъното му (сн.5.16)
Сн. 5.16 Разбъркващ механизъм с потопяем електродвигател
Миксиращият елемент е пропелер, монтиран директно към ротора на електрически двигател, чиято мощност е над 15кW и зависи от обема на ферментатора. Режимът на работа е периодичен и се задава чрез програматор. В качеството на допълнителни аргументи за управление на миксирането могат да се използват температурата, рН на субстрата или концентрацията на биогаз. Високоборотните миксери са адаптивни към всички видове ферментатори, но са технологично пригодни за инсталации, работещи с биомаса с ниско съдържание на влакнести компоненти.
14.3. Хидравлични миксери.
Хидравличното миксиране е интегративно технологично решение, обвързано с помпения агрегат за зареждане, допълнително нарязване (кутиране) и темпериране на биомасата през външен топлообменник (вж. т.13.3). Разбъркващият ефект се постига чрез хидравличен дифузор, свързан към тръбната магистрала на помпения агрегат и външния топлообменник. Самият дифузор е монтиран във вътрешността на ферментатора, върху опорен (петови) лагер, позволяващ завъртането му в равнинен ъгъл от 0 до 300 градуса (сн.5.17)
Сн. 5.17 Хидравличен разбъркващ механизъм с въртяща се дюза
Легенда:
1. Лост за задвижване
2. Подаване (вход)
3. Проход, газонепроницаем
4. Разбъркваща дюза, самовъртяща се, приблизително от 0-300°С
5. Основен лагер
6. Стена на ферментатора.
Хидравличното миксиране е технологично ефективно и сравнително ниско-енергийно. Реализуемо е и при използване на биомаси, съдържащи влакнести компоненти.
15. Системи и съоръжения за съхраняване на добития биогаз.
Безаварийният добив и равномерното подаване на биогаза към когенераторите се определят от подходящо оразмерена и конструирана газ-холдерна камера. В зависимост от конструктивното обособяване на газ-холдера са установени две основни системи за съхранение на добития биогаз [4].
15.1. Газ-холдер, интегриран в конструкцията на ферментатора.
Този подход е най-разпространеният в практиката за производство на биогаз. Газ-холдерната камера е обособена в горната част на ферментатора под формата на сегмент от сфера (сн.5.18).
Сн.5.18. Купол от фолио върху ферментатора за съхранение на газ
Куполът се изработва от специална мембрана от етиленпропилен-термополимер (ЕROM). Мембраната се фиксира към горния ръб на ферментатора по метода „Seeger”. В тази част на стената се монтира обиколен канал със сечение на полукръг. Краят на купола се поставя в канала и се фиксира към него с помощта на еластичен шланг (маркуч). Пълната херметичност между мембраната и канала се постига чрез подаване на флуид под налягане в обема на фиксиращия шланг. В горната вътрешна част на ферментатора (под купола) се монтира решетъчна армировка (скара), предпазваща купола от провисване в началните дни на работа на инсталацията (сн.5.19)
Фиг. 5.19 Дървена конструкция против провисване на купола
Сравнително иновативни са двуслойните и трислойни мембрани, които не се нуждаят от скарова армировка. Газовата камера между двата слоя е със свръх налягане около 30 mbar (милибара), което стабилизара полусферичната форма на купола при недостатъчно газово производство.
Това са усилени полиестерни PVC мембрани [4], устойчиви на UV лъчи и против проникване на въздух (сн.5.20), като мярка за необразуване на взривни смеси.
Сн. 5.20 Трислойна мембрана за съхранение на биогаз
15.2. Разделно съхранение на биогаза с автономен газоходер.
При този технологичен вариант газ-холдера е обособен като самостоятелна камера, инсталирана в непосрествена близост до ферментатора(фиг.5.9)
Фиг. 5.9 Схема на биогазова инсталация с автономен газхолдер
Отделеният в биореактора газ се подава непрекъснато към камерата за акумулиране и временно съхранение. Газ-холдерите се изработват от същия полимерен материал като този на интегрираните куполи. Основно предимство на този вариант инсталации е намаляване съдържанието на водни пари и въглероден диоксид в биогаза. С оглед регулиране налягането на биогаза, автономните камери могат да се оформят като газови „възглавници”, над които се поставя противотежест с регулируема маса. Налягането на биогаза в резервоара е винаги постоянно и не бива да превишава 50 mbar (фиг.5.10).
Фиг. 5.10 Схема на газхолдер тип „възглавница” от полимерно фолио
Легенда
1 - покрив; 2 - натоварваща тежест; 3 -
възглавница за съхранение на газа; 4 -
фундаментална плоча
16. Когенератор
Когенераторът представлява енергетичен модул за едновременно производство на електрическа и топлинна енергия ( фиг.5.11, сн.5.21).
Фиг.5.11 Система за когенерация на биогаз
Сн. 5.21 Когенератор
Концепцията на когенераторния енергодобив се обосновава със следния пример: Коефициентът на полезно действие при съвременните конвекционални електроцентрали (ТЕЦ; АЕЦ и прочие) е в диапазон 40-42% (0.40÷42). При едновременното производство на електрическа енергия и топлина по принципа на когенерацията, коефициентът на полезно действие нараства до 75-85% при съотношение между двата вида енергия 1÷1.5.
Когенераторната система включва три функционално свързани помежду си модула - двигател с вътрешно горене, електрически генератор и топлообменници за отвеждане на отделяната топлина (фиг.5.11)
Двигателят е преустроена бензинова модификация (Ото двигател) за работа с биогаз. Този вариант е основен за инсталации, работещи в мощностния диапазон, от 20 кW до 1 MW. За по-високи електрогенериращи мощности се предлагат когенератори с газово-турбинни двигатели.
Механичната енергия на двигателя задвижва електрическия генератор, който от своя страна индуктира електрическа енергия под формата на променлив трифазен ток. Последният се синхронизира с честотата на мрежовата електроенергия и след съответстваща трансформация се подава към електроразпределителната система.
Топлинната генерация се извършва на две температурни нива. Топлообменниците, свързани към блока и мазителната система на двигателя усвояват топлинна енергия на ниво 80-90°С. Второто топлообменно стъпало е свързано откъм изпускателния колектор на двигателя и утилизира топлината на изгорелите газове с температура 400-500°С. От гледна точка дебита на използваните топлоносители, топлообменниците са свързани последователно. Обикновено усвояваната топлина е разчетена и предназначена за топлопроводни системи с температурен режим 90/70°С.
Годишният експлоатационен режим на когенераторите се залага на 8000 часа непрекъсната работа. По график когенераторите се изключват за годишна профилактика и сервизиране в рамките на 10-15 дни. При посочената схема на експлоатация и съществуващата сега пазарна конюнктура относителните инвестиционни разходи за когенеративните модули се движат в диапазон от 320 до 1270 евро за кWе (киловат електрическа мощност).
Технологични режими за работа на биогазовите инсталации.
Технологичният режим на биогазовите инсталации се определя от броя на ферментаторите, начините на зареждането и свързането им, както и от контрол върху хидролитичните и микробиалните процеси, протичащи в биомасата.
16.1. Биогазови инсталации с един ферментатор.
Добивът на биогаз е съсредоточен в един ферментатор, чието зареждане може да се осъществява в два режима.
✔ Режим на периодично зареждане на ферментатора.
Ферментаторът се зарежда еднократно в целия си обем, след което съобразно възприетия температурен режим, биомасата престоява и ферментира в продължение на период от 20 до 45 дни. Газовото производство в рамките на технологичния цикъл е неравномервно и екстензивно. Това силно ограничава използването на режима при проекти с когенеративна конверсия на биогаза. Технологичната схема на един ферментатор с периодично зареждане е подходяща за обстоятелства, при които единственият приоритет е организирана утилизация на отпадна органична материя, а енергийният добив е под формата на топлинна енергия без предварително заложена финанасова прогноза.
✔ Режим на непрекъснато (поточно) зареждане на ферментатора.
Ферментаторът се зарежда постепенно с биомаса до номиналния си работен обем. Така нормалният технологичен режим се установява в рамките на 2 до 3 седмици, в зависимост от възприетия температурен режим на ферментация. В последствие ежедневно от реактора се отделя „среднодневна” доза от ферментирал субстрат (биошлам) и се добавя същото количество свежа биомаса. При тази схема на работа се постига равномерен денонощен добив на биогаз, което удовлетворява условията за постоянна когенеративна енергия. Този технологичен режим е подходящ за сравнително неголеми биогазови инсталации, изграждани към действащи животновъдни ферми (най-вече кравеферми).
16.2. Биогазови инсталации с два и повече ферментаора.
Инсталациите се комплектоват минимум с два ферментатора в режим на поточно (непрекъсното) зареждане. Технологичната презумпция е да се постигне максимално интензивен добив на биогаз. Спецификата в утвърдените технологични схеми се определя от начина на свързване на ферментаторите към биогазовата инфраструктура и контролът върху биохимизма на ферментиращите субстрати.
✔ Биогазови инсталации с паралелно свързани ферментатори.
Биогазовите инсталации се комплектоват с два или повече ферментатора, които са свързани паралелно към биогазовата инфраструктура, но са функционално независими един от друг. Тази схема на работа позволява да се интензифицира газовото производство и да се осигури максимална гаранция на денонощните дебити от биогаз. Освен това се повишава надеждността на системата спрямо аварийни ситуации във ферментаторите или в обслужващите ги технически съоръжения.
✔ Биогазови инсталации с последователно (по двойки) свързани ферментатори.
Биогазовите инсталации се комплектоват с два, четири или шест ферментатора свързани помежду си последователно по двойки. Технологичната концепция е да се осигури режим на двуфазова ферментация на субстрата. Първият ферментатор от всяка двойка е предназначен да осигури бърза хидролиза и киселинно ферментиране на биомасата. Ежедневно, част от субстрата му се прехвърля във втория ферментатор, където се поддържат максимално благоприятни условия за метаногенеза - т.е протичане на втората фаза от ферментацията. Независимо, че основният добив на биогаз е във втория ферментатор, към инфраструктурната система е свързан и първия.
Технологичната схема за двуфазово разлагане на биомасата в последователно свързани ферментатори е изключително перспективна и е препоръчителна за биогазови инсталации със сравнително високомощностни когенератори.
17. Алгоритъм за определяне на енергийно мощностните показатели на биомаса при когенеративен режим на конверсия на биогаза.
17.1. Определяне на номиналния обем от биомаса за ферментатор с даден брутен обем.
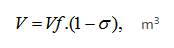
където:
V - номиналният обем от биомаса в брутния обем на ферментатора, m3;
Vf - брутният обем на ферментатора съгласно конструктивните му параметри m3;
σ - коефициент отчитащ ангажирания обем от техническите средства инсталирани във ферментатора (σ≈0.20÷0.30).
17.2. Определяне ежедневния обем от биомаса, необходим за осигуряване на поточен режим за зареждане на ферментатора.
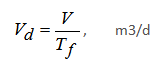
където:
Vd - ежедневно необходимя обем от биомаса, m3/d;
Tf - продължителност на технологичния престой за ферментация на биомасата във ферментатора (дни), d.
17.3. Определяне структурата на ежедневния обем от биомаса.
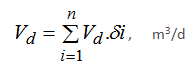
където:
- коефициентът за обемния дял на всеки кофеермент в състава на биомасата (
= 0÷1.0);
17.4. Определяне на среднодневната маса на зареждания обем
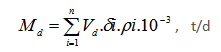
където:
Md - масата на ежедневно зареждания обем, t/d;
- обемната маса (плътността) на съответния кофермент на биомасата, kg/m3.
17.5. Определяне на относителното съдържание на сухо вещество на използваната биомаса.
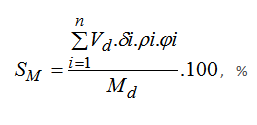
където:
SM - относителното съдържание на сухо вещество в биомасата, %;
- относителният дял на сухото вещество за съответния кофермeнт (φ= 0÷1.0).
17.6. Определяне на средноденонощния добив на биогаз.
където:
Q- средноденонощният добив на биогаз, m3/d;
qi - специфичният добив на биогаз от единица маса на съответен кофермент, m3/kg;
ri - редукционен коефициент, отчитащ технологичните загуби от биогаз (ri ≈ 0.05÷0.10).
17.7. Определяне на брутния денонощен енергодобив.
Ed = Q . e. r2, kWh/d
където:
Ed - брутният денонощен енергодбив, kWh/d;
e - калоричността (енергийността) на добития биогаз (4.5 - 6.0 kWh/m3), kWh/m3;
r2 - редукционният коефициент, отчитащ загубите при енергийната конверсия на биогаза (r2 ≈ 0.05).
17.8. Определяне на потенциалната когенеративна мощност.
където:
- потенциалната когенеративна мощност.
17.9. Определяне на реалната електрическа мощност на когенератора.
Pe = Pk . η, kWe
където:
Pe - реално постижимата електрическа мощност на когенератора, kWe;
η - обобщаващ коефициент на полезно действие на двигателя и електрически генератор (η ≈ 0.27)
17.10. Определяне на реално усвоимата топлинна мощност от когенератора.
където:

Основни понятия :
Литература
- Граматиков П., Възможности за производство на биогаз от твърди битови отпадъци в България,Топлотехника за бита, бр.10, 9-16, 2004.
- Квалих Е., Биогаз, Земиздат,1986.
- Обзор върху проблемите на биогаза, Target GmbHq Germany, 2006.
- Проспект ECOMEMBRANE,Ecomembrane srl, CREMONA-ITALIA
- Пейчев К., Д. Динев, Р. Георгиев, Н. Делчев и др. 2006. Възобновяеми енергийни източници в земеделието (Международен проект “PROAERE” по програма “Леонардо да Винчи”)
- Станев С., Енергията , която идва от слънцето и се „натрупва в растенията, а ние пропиляваме”, Животновъдство плюс, №3, 22-24, 2003
- Станев С., Биогазът - една златна възможност, Фермер, №7, 8-9, 2002.
- Щайнер Т., Получаване на биогаз (биогазов процес), Годишник на Минно-геоложкия университет” Св. Иван Рилски”, Свитък IV, Европейски факултет, XLIII, 53-60, 1988.
- Biogas (Anlagebahn - Foerderung - Praxisbetriebe, Landwirtschaftliches Wochenblatt, №29, 168, 2001.
- Dan K., Anaerobic digestion, Walford College, 2000=
- Reinhold G., Welche Faktoren bestimmen die Wirtschaftlichkeit von Biogasanlagen?, Tagesband zum KTBL/FNR - Biogas - Kongres, 15-16, September, Weimar, 2009.
- Rostalski K., Roehwerke in Biogasanlagen - Technik mit zentraler Bedeutung
- Tagesband zum KTBL/FNR - Biogas - Kongres, 15-16, September,Weimar,2009
Мобилен миксер/самоходен